|
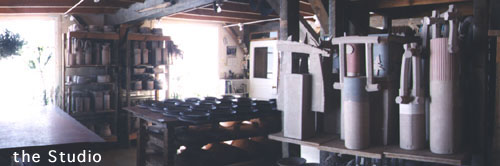
Welcome to the studio. This is where Jon makes his pottery. There are
many steps to making a single completed piece of pottery:
- The clay is prepared. For the stoneware pottery that Jon makes the
clay is a mixture of diferent chemicals and powders as well as natural
clay. Jon has two different formulas for his clay; one for thowing, and
one for hand built pottery. In the next few steps clay is trimed away from
the pieces, to be recycled at this step when the clay is mixed. This is
done by combining all the components in a very large and powerful mixer.
The mixer that Jon uses we he is recycling his clay is actually a industrial
dough mixer.
- The peice is thrown on potter's wheel or hand built. Although this
is the most glamourous part of making pottery it is really just one small
step.
- Right after the peice is thown or hand built, often while it is still
wet, a pre-firing glaze is often applied. This glaze is usually covered
over with other glazes latter which it will react to when fired.
- When the clay has dried to a leathery state the work is trimed, or
additional parts are added to it such as handles or spouts. (Speaking of
which teapots are actually two seperate peices of pottery, the pot itself
and the lid, and each part has to be made seperately.)
- Once the clay is sufficently dry it is fired for the first time in
what is called a "bisque firing". This first firing is done in
Jon's propane kiln. Although this firing is not as hot as the second firing
(the glaze firing) it is still hot enough to heat the fire bricks of the
kiln untill they glow. A firing is a long process, first the kilm is loaded
so that the peices are not touching (if they were they would stick together)
this takes two to three hours. Then the kiln is fired for about eight hours,
during which time the burners must be adjusted to keep the temperature
just right. When the firing is done it takes at least another eight hours
for the kiln to cool down enough to be unpacked, and even then protective
gloves and clothing must be worn.
- After the bisque firing the pots are decoratively glazed. Glaze is
actually silicon based with other chemicals added for colors.
- Once the pottery is dry from the glazing it is fired in the kiln again,
in what is called a glaze firing. It is called this because this is where
the glaze is fused to the pottery. The silicon based glaze and the clay
are heat to such a high temperature that they fuse together, and the glaze
actually becomes a glass coating. As well you may have noticed that Jon's
pottery has spots on it. This is because during the glaze firing the iron
minerals that are in the clay are heated so much that they oxidize and
move to the surface mixing with the glaze. The glaze firing takes longer
that the bisque firing, and thus must be given a longer time to cool down
before it can be unpacked.
- As Jon unpacks his kiln he will grind each pot. What this means is
he will take a special type of stone and grind by hand areas where bare
clay had contact with the shelves of his kiln. This is necessary to take
of any sharp edges that from the bottoms of the pots.
- After this the pots are ready to be cleaned and put into the showroom,
unless they are certain tea pots, paintings, or murals. In which case they
must be mounted and framed, or no clay handles must be attached.
|
|